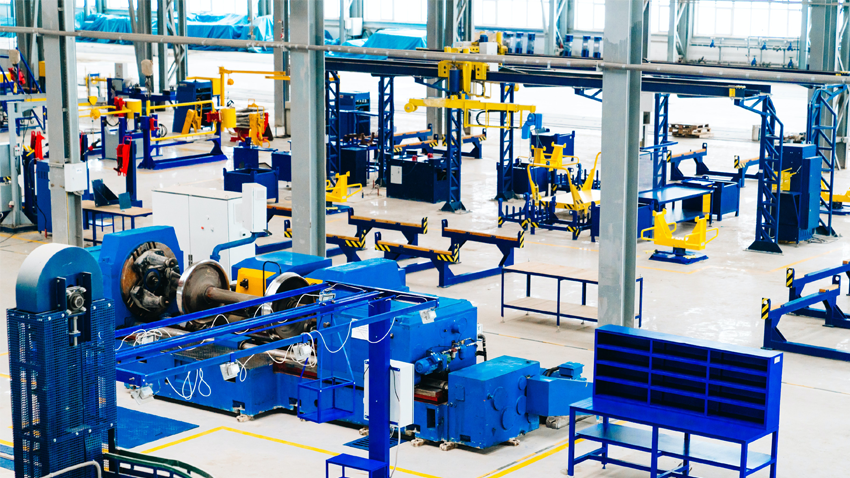
Manufacturing Session
November 18 | 14:30 - 17:50
Break: 16:00 – 16:30
Language: English
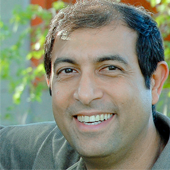
Keynote Speaker
14:30 - 15:00
RevolutionInSimulation.org | Malcolm Panthaki
Simulation at a Crossroads - the Rev-Sim Community Powers Next-Gen Simulation
Simulation is at a crossroads. Many strategic enterprise initiatives such as autonomous driving, additive manufacturing and multidisciplinary optimization need automated simulation by non-experts. This requires the Democratization of Simulation, increasing the number of simulation users and the simulations performed by one or more orders of magnitude. But transitions like this are never simple and the simulation ecosystem is currently navigating through this tipping point.
This exponentially increasing demand for simulation has led to a disruptive “revolution in simulation” and the need for an online, resource-rich community that helps organizations better meet these demands. The free-to-join RevolutionInSimulation community (Rev-Sim.org), launched in 2018, provides professional resources and a collaborative community to help increase the impact and value of engineering simulation software (CAE) investments through the Democratization of Simulation. Here you’ll have access to success stories, news, articles, whitepapers, blogs, presentations, videos, webinars, best practices and reference materials, curated by a number of Topic Moderators, to help you take your simulation investment to the next level. With a steadily growing list of global members, visitors and industry sponsors, the RevolutionInSimulation community is here to stay.
Malcolm Panthaki has over 30 years of experience developing simulation environments to enhance the effectiveness of the product development process, bringing simulation safely and robustly to the entire enterprise. At Abaqus Inc. (acquired by Dassault Systemes) Malcolm led the development of Abaqus/CAE. As an entrepreneur and founder of Comet Solutions and as the founder of the online community, RevolutionInSimulation.org, he has helped reshape the dialog on bringing simulation automation to everyone that needs it, not just the experts. As VP of Analysis Solutions at Aras, Malcolm leads the Aras strategy in the areas of MBSE and Simulation Management and works with key customers and strategic partners to better understand and implement their needs.
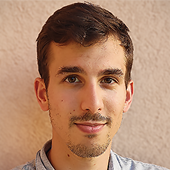
15:00 - 15:20
University of Trento | Matteo Berlato
Flexible stand-up pouch filling process analysis by Coupling Particle-Based CFD and Multi-Flexible Body Dynamics Simulation
In this work, a flexible stand-up pouch filling process is modeled and simulated, focusing on the forming, fluid filling, and sealing stages. The objective of the project is the development of a robust methodology to simulate the behavior of free-surface fluids interacting with highly flexible moving boundaries. The problem is investigated by coupling two commercial simulation tools: Particleworks and RecurDyn. The first represents the fluid behavior by means of Particle-Based (MPS) CFD whereas the latter efficiently calculates the flexible pouch deformation performing a Multi-Flexible-Body Dynamics simulation. The two software are connected using a two-way coupling to obtain an accurate interaction between fluid and flexible boundaries. A real industrial application is studied considering different motion laws, motion ranges, materials, and identifying an ideal combination of these parameters.
Matteo Berlato received a master’s degree cum laude in Mechatronics Engineering from the University of Trento (Italy) in July 2021. He developed his thesis project entitled “Investigating the Interactions of Moving Fluids and Moving Flexible Structures by Coupling Particle-Based CFD and Multi-Flexible-Body Dynamics Simulation” in collaboration with EnginSoft Spa. Passioned about CAE tools and their application in industry, he has just started his career in this field.
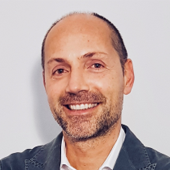
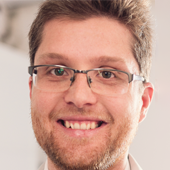
15:20 - 15:40
Quin | Francesco Falcolini
ESTECO | Alessandro Turco
Data-driven optimization of Business Processes
The digital twin is an established technology in the engineering field. On the contrary, the digital twin of an organization is still more a promise than a reality because it is difficult to model, measure and analyze human behavior. Effective digital transformation starts with evidence-driven methods to identify how our processes work. The key to success is the combination of field expertise and state of the art computational techniques.
We prove this statement considering a typical process of a bank. The process has been digitalized and hence it is possible to use Process Mining techniques to extract data and information. With the help of process experts, we set up a simulation model able to reproduce the original process and to test possible variations. Optimization software can link simulation scenarios to business KPIs and returns a suitable Pareto frontier. Process experts maintain the responsibility on the final decision while a detailed dashboard highlights gains and savings.
Curriculum F. Falcolini | Curriculum A. Turco
Francesco Falcolini is Business Analytics Director at Quin, Italy.
With a degree in Physics at Federico II University in Naples, he's also got PMP, PRINCE2, COBIT and ITIL certifications.
In his work, he combines data analytics techniques such as business intelligence, data warehouse and machine learning with his 20-year old experience in Project Management and IT Governance. In his career, he recently developed a strong interest in process mining.
Alessandro Turco has a PhD in Applied Math from the International School of Advanced Studies (SISSA) of Trieste and a Master in Management from the School of Management of Milan Polytechnic (MIP).
He has been working for ESTECO SpA for ten years, starting as a researcher for the Numerical Method Group. He is now the project manager of Cardanit, the BPM solution from ESTECO.
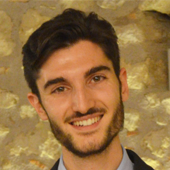
15:40 - 16:00
Meccanica Cainelli | Alessandro De Mori
The impact of MAGMASOFT Automatic Design Optimization on the preliminary evaluation of the correlations between HPDC parameters and casting quality
The combination between lightweight materials, such as Al-based alloys and advanced manufacturing processes, like High Pressure Die Casting (HPDC), can promote the implementation of advanced on-board control systems in automotive without penalizing the overall weight of the vehicle. These devices, mainly referred to emission control and safety monitoring systems are becoming increasingly important for Hybrid Electric Vehicles (HEVs), Plug-in Hybrid Electric Vehicles (PHEVs) and Battery Electric Vehicles (BEVs). This paper, developed within SMARTI 4.0 project, presents the results of a study carried out through the Autonomous Engineering package supplied by MAGMASOFT® 5.4. The objective is to define the best positions of temperature sensors in an HPDC mold. By means of Design of Experiments methodology and Autonomous Optimization, the correlation between the main process parameters and the casting quality has been assessed. Some of the results of the automated virtual test plan will be adopted to pursue different quality results on a CCU, an on-board charger system for battery packs in hybrid and pure electric vehicles, used as industrial demonstrator.
Alessandro De Mori is currently working as a project engineer in an aluminium high-pressure die casting foundry operating in the automotive sector. In his work, he combines project management techniques together with the knowledge of the foundry processes to coordinate the activities of new projects, from the feasibility analysis to the Start of Production phase. Alessandro is also part of the R&D team of the company, being involved in the SMARTI4.0 project, focused on smart manufacturing for an automotive tier.
After taking the master’s degree in Mechanical Engineering at the University of Padova, he received his PhD in Mechanical Product Innovation Engineering defending a thesis focused on the development of secondary aluminium alloys for high-temperature applications.
16:00 – 16:30 BREAK
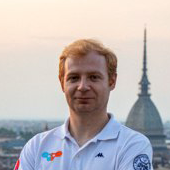
16:30 - 16:50
Politecnico di Torino | Marco Francesco Ardemagni
Design, Optimization and Manufacturing of an Aluminium Wheel Rim for an Urban Vehicle
The paper describes the topology optimization of a customized Al6062 T6 wheel rim for the Urban Concept JUNO, a low consumption vehicle, which participates in the Shell Eco-marathon competition. Starting from tyre dimensions (Michelin 95/80 R16) a first CAD has been made, followed by a topological optimization. The load case to design the wheel rim corresponds to vehicle rollover and to tyre inflation pressure up to 6 bars. The result was obtained through the setting of the topological variables in FEA simulation, choosing stiffness maximization with the less mass possible.
The final component, realized using 3-axis CNC machines, has a mass of 2,9 kg, considering a safety factor of 3.5.
Master Degree student in Mechanical Engineering at Politecnico di Torino.
As Team Manager of Team H2politO (https://areeweb.polito.it/didattica/h2polito/) student team I coordinate the activities of our technical departments in order to compete at Shell Eco-marathon with two vehicles.
As educator at the Museo Nazionale dell’Automobile di Torino I teach to high school students new trends in automotive industry and road safety.
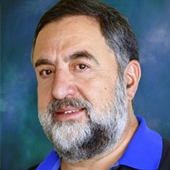
16:50 - 17:10
AES | Andreas Vlahinos
Design Process for Architected Materials
Metamaterials or Architected Materials are structural configurations of repeating patterns that have material properties not found in natural materials. The shape, the geometry, the topology, the size, and the combination of conventional material give metamaterials their tunable properties. Metamaterials can be designed to have negative Poisson’s ratio, that are great for ballistic protection and radar avoidance, or zero coefficient of thermal expansion, that are great for stress reduction on environments with high thermal gradients. Other applications of tunable metamaterials can be found in optical filters, high-frequency battlefield communication devices, medical devices, sensors, energy absorption devices, radomes with negative permittivity and permeability characteristics, etc. The advances in additive manufacturing, lattice generation tools and the multi-material metallic printers enable the manufacturing of metamaterials. The challenge is to conceive, design and validate metamaterial concepts. In this presentation the recent progress in lattice generation tools coupled with optimization techniques will be outlined. A practical metamaterial discovery process that generates a near zero coefficient of thermal expansion material will be demonstrated.
Dr. Andreas Vlahinos is a CTO of Advanced Engineering Solutions and EnginSoft USA.
Andreas has concentrated on DfAM, Computer Aided Innovation, Generative Design, Lattice Structures, Simple Solutions to Complex Problems. He has been instrumental in rapid product development through the implementation of Design For Six Sigma (DFSS) and Computer Aided Engineering for several Government agencies such as NASA, NREL, SANDIA, DOE, NCDMM and US Army Aviation & Missile Command and several industry partners such as SpaceX, General Dynamics, United Launch Alliance, NAVISTAR Defense, etc. He has been Professor of structural engineering at the University of Colorado. Several times he received the Professor of the Year Award.
He has received the R&D 100 award and several patents. He received his Ph.D. in Engineering Science and Mechanics from Georgia Institute of Technology.
Finally, he is regularly invited as a keynote speaker on a variety of subjects (Generative Design, Innovation, DFSS, DfAM, IoT) in international conferences.
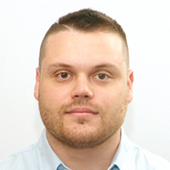
17:10 - 17:30
RINA Consulting | Diego Cioccari
Development of models for calculating the mechanical characteristics of 3D printed metal components
The capability to handle various materials and the possibility to create different shapes make Additive Manufacturing a process in strong growth. However, the variability induced to the final mechanical properties must be considered since these depend on the process parameters and final shapes. This variability influences the distribution of the thermal gradients, which impacts on the mechanical characteristics of the products. The aim of this work is to create a numerical model to foresee the influence of the process parameters on the final mechanical properties. The proposed model is showcased for the Selective Laser Melting process and it is verified against experimental results: a database of the properties of the produced pieces is thus created to estimate the final properties. This tool can support the design phase during the Computer-Aided Engineering analyses, in fact such a model allows to identify the combination of process parameters to ensure the desired properties for the final product.
Diego Cioccari works as Analyst in the Industrial Design & Computer-Aided Engineering (CAE) team at RINA.
He earned a master's degree from the University of Rome "Tor Vergata" in 2020 with a thesis on the modeling of additive manufacturing processes for the prediction of the mechanical characteristics of the printed pieces.
In RINA Consulting SpA, he gained experience in the field of CAE, with focus on FE Analyses with tool of Ansys®, CAD modeling with SpaceClaim® and Solidworks® and data analysis with Python programming language.
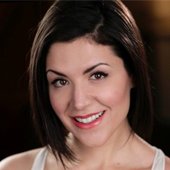
17:30 - 17:50
nTopology | Erica Vlahinos
Accelerating Innovation with Implicit Modeling and AM
Soap bubbles, catenoidal soap-film surfaces, gyroids in butterfly wings and Nautilus sea shells are some examples of complex but effective geometries in nature. These complex geometries are minimal surfaces. In the early seventies, mathematicians discovered the mathematical expressions of minimal surfaces. These surfaces were not used in product design since we couldn’t generate these designs in CAD and we couldn’t manufacture them. The recent advances in AM and Implicit geometric modeling enable engineers to accelerate the pace of innovation by giving them the ability to design and manufacture these amazing geometries. In this presentation a brief introduction to implicit modeling and several examples of high-performance, innovative designs will be demonstrated.
Erica Vlahinos is a Technical Account Manager specializing in DfAM tools. In parallel to her work in the additive industry, Vlahinos is a NYC based playwright and performer whose original works have been seen Off-Broadway and regionally.
Vlahinos' experience as a Playwright and as an Account Manager, having advised over 300 companies on additive software strategies, has provided her with unique insight into the nature of technical innovation and the creative processes behind it.